
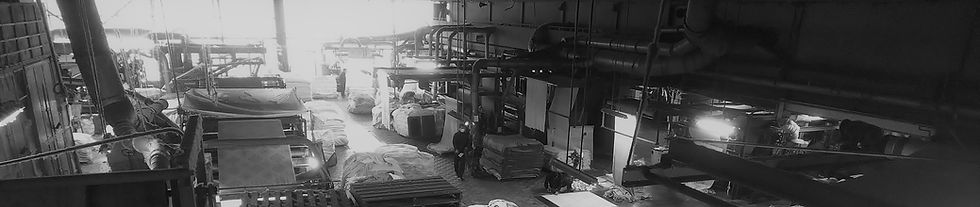_JPG.jpg)
factory

スクリーンプリント
センターカットされた生地の上にスクリーンをのせ、その上に染料を入れます。そして、スクリーン内のスケージ(金属の棒)が動き、版画のように生地へ染料が刷り込まれていきます。
生地によりますが、スクリーンは全部10枚まで取り付けることができます。1枚につき1色分しか染料が入らないので、原理上は10色しか使えませんが、それ以上の色数を使ってプリントすることができます。実際、モナリザの毛布は16色使用しています。
そのための技法としては‘重色'、‘抜染'、‘グラデーション'の3つあります。重色は色を重ねる、つまり赤色に染色された生地の同じ箇所に青をのせて紫にします。抜染は色を抜いて染める手法で、糊を先に上にのせた後で染料をのせることで色濃度が薄くなります。グラデーションは染料が生地に全て浸透していかないようにスクリーンに細工しています。
グラデーションの手法はスクリーンを作る技術も不可欠です。その技術も年々進歩しています。例えば、元々は手彫りでスクリーンを製造していましたが、近年では写真や画像をそのままコンピューターに取り込んで作る方法も開発されました。
モナリザ絵画をそのまま毛布にできるレベルまで、上記の手法を使いつつ繊細な部分まで染色によって表現ができるのは日本ならではの技術です。
連続染色機
連続染色機は主にアクリルなどの合成繊維を無地で染める際に使われます。連続的に流れていく形で生地を染色していくため、この名がつけられています。
染料が入った浴槽へ生地を浸漬する形で染めます。そのあと、余分な染料を絞った後にスチーム機へ連続で入っていきます。


オーロラ染色機
連続染色機内に、染料を生地にスプレーで吹き付けて染色する‘オーロラ染色機'を備えています。
生地の基布側からスプレーを吹き付けることで、毛先の部分が染まらない白地が残るため、霞みがかったオーロラのような見た目の毛布にすることができます。
スプレーの当て方を変えることで様々な模様パターンを出すことができます。基布側だけでなくパイル側から染料を吹きかけることもあります。
ウィンス染色機
ウィンス機は綿毛布を無地で染める際に使われます。
国内でも扱う所が少ない珍しい染色機で、ループ状につないだ生地を回転させながら、染色槽の中に浸して染色する機械です。
綿の場合は天然繊維なので、色むらになってしまうのを防ぐため、この染色機を使って徐々に温度を上げつつ色をつけています。
また、染色の前にアルカリ性の熱湯につける‘精錬'という工程を行います。綿は元々の黄色い色素や油分を含んでいるため、そのまま染めるとくすんだ色合いになってしまいます。なので精錬により白くし染まりやすい状態にしてあげます。
ウィンスによる染色は生地にかかる張力が緩やかなので、生地の持つ質感を損なわず染めることが可能です。綿本来の質感を最大限に生かしたふわふわの綿毛布に仕上げることが出来ます。
-min.jpg)

スチーム
連続染色機もしくはスクリーンプリントによる染色後に、スチーム機によって100℃の温度で生地を蒸します。蒸す理由としては主に3つあります。
1つ目にパイルが抜けなくなることです。基布の地糸では高収縮のポリエステルを使用し、鎖糸は約13%熱収縮します。基布の鎖糸の輪っかが締まり、パイルが固定されます。
2つ目に染料を定着させることです。熱が加わることで、染料と生地がしっかりと結びつき、洗っても色が落ちないようになります。
3つ目が、アクリルの熱によるバルキー収縮をかけることです。バルキー収縮によってふっくらとした毛布に仕上げることができます(詳しくは>>アクリルの暖かさの秘訣)。
洗い・乾燥
スチーム機から上がった状態では染料は生地に定着しましたが、染料内に含まれている糊が残っています。そこで、水流を起こすローラーが搭載された5層の洗い機で丁寧に糊を落としていきます。
最後の浴槽には柔軟液を入れ、毛布にコーティングすることで、毛布の軋みを無くし肌触りがなめらかになります。他には、抗菌防臭や花粉などを落ちやすくする等の機能付与や、ローズオイル, 椿オイル, シルクプロテインなどを配合する特殊加工を柔軟層で施しています(より詳しく>> 特殊加工の取り扱い種類)。
洗いの後は、約120度の乾燥機に約20分通していきます。洗い後の毛布の状態は生地が縮んでいるので、ピンテンターで幅を広げつつ乾燥させていきます。